Australian automotive tradesperson placement agency Techs on the Move is launching a new candidate pool service to the industry. See here to read this recent feature from AutoTalk
Category: News
Why do we accept inefficiency in our workshops?
Why is it that some Service Managers focus on how little they can pay their technicians, yet rarely look at the opportunity cost associated with them standing at the back counter waiting for parts or fumbling around in a congested car park. Regrettably many dealerships accept inefficient work practices, and have previously relied on increasing their labour rates, or upselling add-ons to attain their budgets. With most manufacturers now moving towards capped price servicing, and focusing on fixed-right-first-time scores, such practices are no longer feasible, and as a result, many dealer’s bottom lines are suffering. I recently visited a mainstream dealership and listened to a service advisor attempting to upsell a rotate and balance and a wheel alignment. Meanwhile, in the workshop I noticed a social gathering of technicians at the parts back counter, presumably waiting on their quotes for additional spare parts, or the indeed the parts themselves. Outside there was a congested car park, where I witnessed a technician wandering around clutching a remote key, holding it in the air and repeatedly pressing the remote in the hope they could identify the vehicle. Once found, they then had to return to service reception to find the keys for the two cars blocking this one in. All up, this technician spent around 15 mins getting their vehicle from the car park, to their work-bay, and then spent another 10 minutes at the parts back counter waiting for their parts. I did some very quick mathematics and my findings were startling. If we consider conservatively that each technician spends 15 mins per job procuring the vehicle and the parts, and works on say four vehicles per day, then an hour of their day is wasted in time that could otherwise have been charged out at upwards of $135, or thereabouts. Then consider that there are 15 technicians working at this dealership, and all of a sudden, we’ve squandered $2,025 of labour that day, or $42,525 for the month. Granted, it’s unlikely we can eliminate this non-value added time altogether, but what if we could reduce it? Furthermore, what about the additional parts we sell, for every extra hour of labour we sell? This incremental labour isn’t a gross sales figure, it actually goes straight to the bottom line, since you’re already paying the technician’s wages. Are manufacturers standard repair times unrealistic, or have we just accepted hundreds of inefficiencies associated with our current practices? The shrewd service manager will have already realized that survival means reducing every ounce of non-value added time from their workshop. This might mean employing parts runners to deliver parts to the technician’s bay, or vehicle-jockey’s to maintain an orderly carpark. It may include educating and training all involved in the importance of labour efficiency and recovery. Identifying any activity that acts as a road block and slows your technicians down. It’s also critical you employ technicians who understand your product, and can apply their experience in ensuring the most efficient rectification possible. Extended service intervals mean less maintenance work and technological advancements mean more diagnostic work.When combined, efficient work practices and employment of highly skilled technicians has never been more important than it is today. Techs On The Move source technicians who are simply, ‘Plug and Play’, that is they’ll hit the ground running, know your product, and already possess the manufacturer training and experience you desire. http://159.65.10.85/ Now none of what I’ve written is rocket science, and most of this has been known since Adam was a boy, so why is it then that inefficient practices remain? I believe it comes down to the fact that having an efficient workshop is a culture, it takes years to cultivate, and requires that everyone is committed to it. There is no one silver bullet, but rather, a hundred small initiatives which when accumulated make the difference between those that will survive, and those dinosaurs who will become extinct, blaming the manufacturers for their unrealistic standard repair times, or capped price service initiatives.
457 Visa cost blowout looms
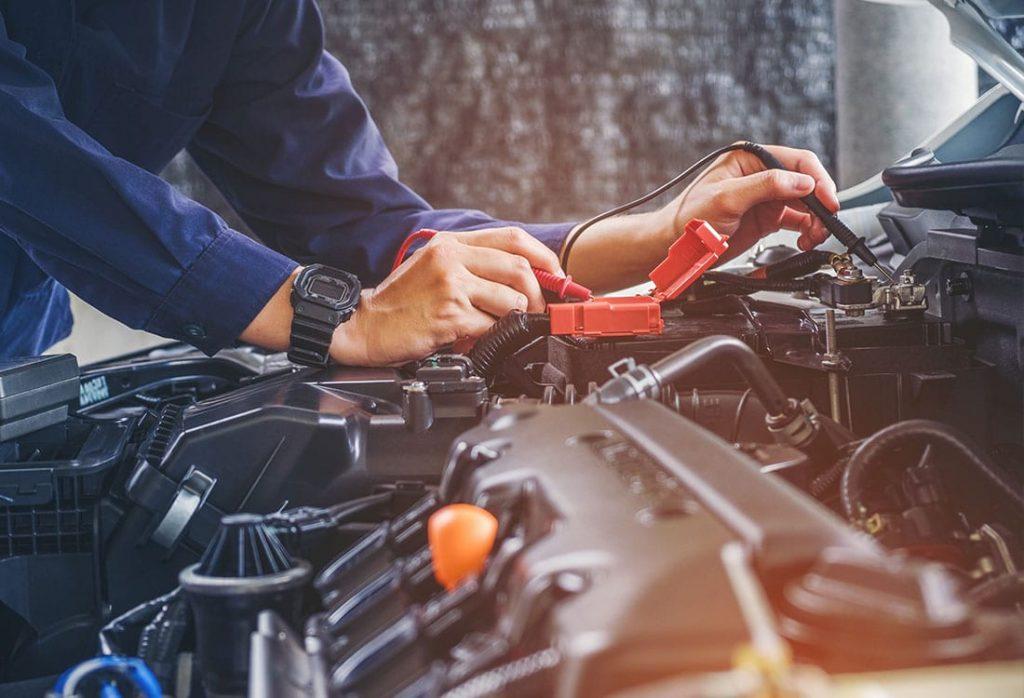
AUSTRALIA’S automotive sector will bear the financial brunt of the federal government’s proposed higher visa charges just to fulfil a massive skills shortfall – estimated at around 35,000 positions – currently being experienced in trades including diesel and motorcycle mechanics, panel beaters and spray painters.
The proposed changes to the 457 Visa system, to be implemented next month, will raise the cost to dealers and repair businesses to $20,000 per worker from the current rate of $12,000.
The increase is due to the government’s plans to put the $8000 difference towards the national apprenticeship scheme, called the Skilling Australians Fund Levy (SAF).
Industry representatives, including the Australian Automotive Dealers Association (AADA) and the Victorian Automobile Chamber of Commerce (VACC), do not have a problem with that allocation of funds but it comes at a bad time with other revenue and margin challenges looming across motor businesses this year.
AADA CEO David Blackhall indicated that the increase in costs will aggravate businesses struggling to maintain their income stream after they have already been shaken by a rash of intrusive charges and changes to their financial income in 2017.
Gavin Stocks from Techs On The Move, who works exclusively with the automotive industry and is an Australian registered migration agent, said automotive businesses aiming to employ migrants need to be aware of these changes.
He told GoAutoNews Premium that he thought that the industry bodies – the AADA, VACC and the Federal Chamber of Automotive Industries (FCAI) – could have done more last year to lobby the government against the rising charges when the changes to the 457 program were mooted.
But Mr Blackhall said discussions started mid-2017 with the minister for immigration and border protection, Peter Dutton, with the aim of reducing the financial impact and improving the skills availability to the automotive industry.
Mr Blackhall said the minister was keen to meet industry representatives but the discussions were interrupted and could not be continued as Mr Dutton was embroiled in the refugee relocation issue. At the same time, the car industry bodies were heavily involved in changes to regulations from Australian Securities and Investments Commission (ASIC) and the Australian Competition and Consumer Commission (ACCC).
He said it was regretful that the meetings with Mr Dutton could not take place. He added that the minister was primarily concerned with people abusing the 457 system which led to people overstaying the temporary visas.
“In addition to our direct representations to the federal government, we have also leveraged our relationship with the Australian Chamber of Commerce and Industry, which has been very active in Canberra in calling for these costs to be brought down,” Mr Blackhall said.
“While we are disappointed with the outcome of this particular policy, to say that we did not expend any effort in making our case to the government is wrong.
“We recognise that the government was primarily concerned with people abusing the 457 system and overstaying their temporary visas.
“Right now, according to the MTAA, there are about 35,000 jobs in the industry that are vacant.
“This is hard on dealers and repair businesses and the extra $8000 they will need to find to support a migrant visa applicant will not help.”
Mr Stocks told GoAutoNews Premium that he was concerned that dealers are “paying twice”.
“They will be paying the $8000 levy plus they are already supporting the national apprenticeship scheme through their own staff.
“It’s a double dip,” he said.
“I think they should be exempt. But there are no exemptions. I believe the industry bodies could have done more.”
Mr Stocks said that while the levy was a blow to dealers and repairers, at least it was being directed at helping to fund a solution to the problem of the shortage of technical labour.
“I know that the feedback from the bigger dealer groups is that we have to do this. They need the labour and without that their businesses may not be as profitable.
“Dealers need the staff because it is very costly when their equipment – such as a hoist or other workshop equipment – is left idle. So (from that point of view) it’s a win-win for the dealers, the migrants and the customers.”
He said that after 20 years of skills shortage, the situation was not improving.
“We still need skilled workers,” he said.
“We actually need skilled workers more now than before because newer cars have sophisticated technology and we are finding that there’s not enough locals to fill the training gaps.
“There are skilled technicians overseas who are working on the modern technology so it seems natural that we can bring them into Australia. But it appears the government isn’t taking the same attitude.
“There is also the case where technicians and other automotive workers are leaving the industry either because of low wages or because there are more attractive opportunities for wages and career, such as the resources industry.”
Mr Stocks said Australia is in the position now where 1000 successful Visa applicants are entering the country yet 500 people in the industry are leaving each year.
His concerns were backed up by a 2017 report by the Victorian Automobile Chamber of Commerce in conjunction with the Motor Trades Association of Australia.
The report, called Directions in Australia’s Automotive Industry, surveyed 1100 Australian automotive businesses on skill shortages by occupation for 2018. It is the largest automotive business survey ever conducted and has a margin of error of only three per cent.
The VACC said that responses received through the survey indicated that 45.7 per cent of automotive businesses are currently experiencing skill shortages – which is the highest proportion recorded over recent years.
“The results show that for 2016/17, there is an estimated total shortage of 27,377 skilled personnel across the automotive industry,” it said.
“This shortage is forecast to grow to 35,083 during 2017/18, before moderating slightly to 31,202 in 2018/19. These estimates are based on current skill shortages as reported for 2016/17 and business demand and labour supply forecasts over the next two years as recorded within the survey.”
The report said the skills shortages were widespread across the automotive industry “however occupations within the automotive repair and maintenance sector are in highest demand”.
“Shortages of light vehicle mechanics are critically high, with a national shortage of 12,943 in 2016/17, rising to 16,656 positions in 2017/18, before declining to 14,799 in 2018/19,” it said.
“Other key skill shortages include vehicle spray painters and panel beaters (2320 and 2304 respectively), motor vehicle salespersons (2243), heavy vehicle mechanics (1973) and automotive electricians (1530).
“Survey respondents have identified vehicle painters as being the second highest occupational skill shortage within the automotive industry, behind motor mechanics.
“In the survey, 64 per cent of respondents rated vehicle painters as a critical skill shortage over the next three years or more.”
Background:
Australia’s 457 visa has been a system for businesses to sponsor skilled overseas workers to work temporarily in Australia.
It will be abolished next month and replaced with the temporary skill shortage (TSS) visa that will offer three options:
- Short-term stream for employers to source genuine temporary overseas skilled workers in specific occupations for a conditional maximum of four years
- Medium-term stream for employers to source highly-skilled overseas workers to fill medium-term critical skills in occupations included on a specific list for up to four years, with eligibility to apply for permanent residence after three years
- Labour Agreement stream for employers to source overseas skilled workers in accordance with a labour agreement with the Commonwealth, on the basis of a demonstrated need that cannot be met in the Australian labour market and where standard visa programs are not available, with the capacity to negotiate a permanent residence option.
From July 1, 2012, non-resident workers on the 457 skilled immigration visa were able to transition to permanent residency if they had two years with the employer who has sponsored them and if the employer provided a full-time position in the 457 visa holder’s nominated occupation.
The federal government reported that as of June 30, 2016, there were 94,890 primary visa holders in Australia.
But in an audit by the Fair Work Ombudsman conducted between September 2013 and June 2014, it was found that 40 per cent of 457 visa holders were no longer employed by the sponsor or were being paid well below the statutory minimum wage of $53,900.
This caused the concern by the federal government about the legitimacy of the scheme and led to the changes that will be introduced next month.
By Neil Dowling